
제조조건에 따른 활성탄의 특성 및 수은 흡착 효율
Copyright © 2015 Korean Society for Atmospheric Environment
Abstract
There is an adsorption method using activated carbon as a typical method for removing elemental mercury. Physical characteristics of activated carbon such as specific surface area and volume of pore (micro and meso) have positive effect for mercury adsorption. Activated carbon is carbon-based material with a high specific surface area. This activated carbon can be manufactured through carbonization and activation process. In this process, physical characteristics of specific surface area and pore distribution are changed by controlling operating parameters like temperature, time and reagent of activation. In this study, we evaluated characteristics of activated carbons manufactured from pinewood and coal with the operating parameters. We evaluated mercury adsorption capacities of the activated carbons having excellent physical characteristics and compared those to the commercial activated carbon.
Keywords:
Activated carbon, Pinewood, Coal, Mercury1. 서 론
연소시설에 사용되는 화석연료, 폐기물 등에는 수은이 존재하므로, 연소시설은 대기 중으로 배출되는 가스상 수은의 대표적인 발생원이다 (Kang et al., 2012). 수은은 연소 배기가스 중에서 원소수은, 산화수은, 입자수은 세 가지 형태로 존재하는데, 이 중 원소수은은 반응성이 낮아 기존 대기오염제어 설비를 통해 제어하기에는 어려움이 따른다. 원소수은을 제어하기 위한 대표적인 방법으로 활성탄을 이용한 흡착방법이 사용되고 있으며, 국외에서는 이미 수은흡착용 활성탄이 상용화되어 사용되고 있다. 국내에서는 수은의 배출 및 분포특성과 촉매를 이용한 원소수은 산화에 대한 연구가 진행되었고 (Hong, 2013; Park, 2008; Lee, 2004), 황, 요오드, 염소와 같은 화학물질을 첨착한 활성탄의 수은 흡착성능을 평가한 연구가 진행되었다 (Ahn, 2004; Cha, 2002). 그러나 여전히 국내에서는 수은 흡착용으로 상용화된 흡착제가 없어, 이에 대한 활발한 연구가 제조조건에 따른 활성탄의 요구되고 있는 시점이다. 활성탄은 높은 비표면적을 지닌 탄소로 구성된 물질로써, 주로 기상 및 액상의 오염물질 제거용도로 사용되고 있다.
활성탄의 제조는 크게 탄화공정과 활성화공정으로 나뉘며, 제조공정의 인자에 따라 제조된 활성탄의 비표면적, 기공분포와 같은 물리적 특성이 크게 달라진다. Kim (2008)은 잣나무와 리기다소나무 폐벌목을 이용하여 350∼600˚C 온도와 15∼90분의 시간범위에서 최적 탄화조건을 도출하였으며, 이후 수산화칼륨과 수산화나트륨을 이용한 화학적 활성화를 통해 활성탄을 제조하였다. 그 결과 가장 높은 요오드흡착능과 비표면적을 나타낸 최적 탄화조건은 두 목재 모두 탄화온도 500 ˚C, 유지시간 60분으로 나타났다. Ghani et al. (2013)은 고무나무 톱밥을 이용, 탄화시간 60분으로 고정한 채 450∼850˚C의 열분해 온도에 따라 생성되는 탄화물의 특성을 분석하였다. 제조된 탄화물의 이산화탄소 (CO2) 흡착량을 분석한 결과 열분해 온도 450∼650˚C의 구간에서 온도가 높아질수록 CO2 흡착량이 더 높아졌으며, 이후의 열분해 온도에서는 CO2 흡착량이 감소하였다. Rambabu et al. (2013)은 석유코크스를 이용하여 별도의 탄화공정 없이 수증기 활성화를 통해 활성탄을 제조하였다. 활성화 온도 900˚C에서 9시간 유지한 채 10∼17.5 g/hr의 범위에서 물 주입량의 영향을 살펴본 결과 물 주입량 10∼15 g/hr에서는 물 주입량 증가에 따라 비표면적이 증가하였으며, 15 g/hr 이상에서는 비표면적이 오히려 감소하였다. 또한 물 주입량 15 g/hr와 유지시간 9시간으로 고정한 채 600∼1000˚C에서 100 ˚C 간격으로 활성화 온도의 영향을 살펴본 결과 600˚C에서 900˚C로 증가함에 있어서 비표면적이 250 m2/g에서 482 m2/g으로 증가하였으나 1000˚C에서는 463 m2/g으로 감소하였다. 따라서 문헌의 결과들을 종합하여 보면, 탄화물은 탄화온도, 탄화시간에 영향을 받았고, 탄화공정이 활성화공정을 거친 활성탄의 물성에도 영향을 미치는 것으로 나타났다.
제조된 활성탄으로 수은 흡착시험을 수행한 결과들을 보면, Skodras et al. (2007)은 소나무, 오크, 폐타이어, 올리브 씨를 원료물질로 하여 물리적, 화학적 활성화를 통해 활성탄을 제조하였으며, 질소배경 하에 50˚C에서 수은 흡착을 진행하였다. 그 결과 제조된 활성탄의 비 표면적과 미세기공이 증가함에 따라 수은 흡착력 또한 증가하는 추세를 나타내었다. 국내 연구진 중에서 Lee and Park (2003)은 상용화된 활성탄을 30˚C, 질소분위기 하에서 수은 흡착을 진행하였다. 그 결과 작은 기공 직경을 가진 활성탄은 수은 분자의 내부 확산을 저해하여 낮은 수은 흡착 효율을 보이지만, 다량의 산소작용기를 가지는 경우 상대적으로 높은 수은 흡착 효율을 나타내었다. 이상의 연구들은 실험실에서 제조된 활성탄을 수은 흡착에 이용하였다는 점에서는 의미를 가지지만, 활성탄이 실공정에서 적용되는 조건과는 거리가 먼 온도와 가스조성에서 시험을 하였다는 한계점이 있다.
본 연구에서는 활성탄 제조에 많이 이용되는 원료물질인 톱밥과 석탄을 이용하여 수은 흡착용 활성탄을 제조하고자 하였다. 원료물질, 탄화온도, 탄화시간, 활성화 온도, 활성화 시간, 수증기 주입량의 변화에 따라 생산되는 활성탄의 비표면적과 기공 분포도를 분석함으로써, 제조조건에 따른 활성탄의 물리적 특성을 조사하였고, 우수한 활성탄을 제조하기 위한 최적의 제조조건을 도출하였다. 또한 최적의 조건에서 제조되는 활성탄을 국외에서 상용화된 수은 흡착용 활성탄과 수은 흡착 효율을 비교하여 국내 수은 흡착제 개발을 위한 기초자료로 활용하고자 하였다.
2. 실험 장치 및 방법
2. 1 시 료
활성탄 제조를 위한 원료물질로는 가장 보편적으로 사용되고 있는 톱밥과 석탄을 이용하였다. 톱밥은 국내 수종 중에서 가장 많이 분포하고 있는 소나무 (red pine, 지엘파크)에서 나온 것을 사용하였다. 수은 흡착용으로 상용화된 활성탄으로는 Norit사의 GL-50을 사용하였다.
소나무톱밥과 석탄시료에 대해서는 열분석기 (Q600, TA instrument)를 이용하여 공업분석을 수행하였으며, 표 1에 성분의 분석 결과를 자세히 나타내었다. 그리고 소나무톱밥은 휘발성분 함량이 많고, 재의 함량은 적은 특성이 있으며, 석탄은 상대적으로 휘발성분 함량이 적고, 재의 함량이 많은 특성이 있다. 열분석기를 이용한 공업분석 과정에서는 온도를 승온시키며 시료의 무게 변화를 측정하게 되므로, 이 결과를 온도에 따른 시료 무게 변화로 나타내면 그림 1과 같다. 그림에서와 같이 소나무톱밥 시료는 300˚C 부근에서 시료 무게가 급격히 감소하는 반면에 석탄 시료는 400˚C부터 시료 무게가 조금씩 감소하는 특성이 있다. 이는 셀룰로오스 (cel-lulose), 헤미셀룰로오스 (hemicellulose), 리그닌 (lignin)과 같은 식물질을 구성하는 복합체는 약한 에테르결합으로 열저항성이 낮은 반면에, 석탄은 높은 결합에너지를 지니는 방향족 탄화수소 결합으로 되어 있어 상대적으로 열저항성이 높다 (Vuthaluru, 2003). 따라서 석탄은 소나무톱밥에 비하여 높은 탄화온도가 필요할 것으로 예상된다.
2. 2 활성탄 제조
활성탄 제조에 사용한 장치는 그림 2에서 보는 바와 같이 로타리 킬른식 반응기로 시료의 균일한 반응을 도모하였다. 원료물질 시료가 위치하는 반응기 내부는 길이 25 cm, 외경 15.5 cm의 규격을 지니도록 설계하였다.
원료물질로부터 활성탄을 제조하기 위해서는 탄화와 활성화공정을 거쳐야 한다. 탄화공정 동안에는 원료물질 내 고정탄소 성분을 제외한 휘발성분의 제거가 요구되므로, 반응기 내부를 지속적으로 비활성 분위기로 유지할 필요가 있다. 또한 반응기 내에 열공급에 따른 승온과정에서 발생되는 휘발성 가스를 지속적으로 외부로 배출시켜야 한다. 따라서 본 실험에서는 탄화공정 동안 질량유량조절기 (MFC, mass flow controller, Brooks Instrument, USA)로 4 L/min 질소가 일정하게 흐르도록 하여 반응기 내부를 비활성 분위기로 유지하면서 휘발성 가스를 반응기 외부로 배출시켰다.
탄화공정에서 활성탄의 물리적 특성을 결정하는 주요 인자는 탄화온도 및 탄화시간이다. 이 두 인자는 서로 독립적이지 않고 연관성이 있으므로, 최적인자 선정 시 하나의 인자를 고정한 후, 다른 인자의 조건을 변화시키면서 최적조건을 결정하였다. 탄화온도는 열분석을 통해 유추한 적정 탄화온도를 기점으로 50˚C 또는 100˚C 간격으로, 탄화시간은 0.5시간 간격으로 변화시 키며 탄화공정을 수행하였다. 제조된 탄화물은 KS M 1802 활성탄 성능 평가 방법 중 요오드 흡착법을 통해 요오드 흡착능을 구하였다.
탄화실험을 통해 최적 탄화조건을 결정한 이후, 최적 탄화조건에 활성화 조건을 변화시키면서 활성탄을 제조하였다. 탄화가 끝난 이후에는 질소가 수조를 통과하게 하여 반응기 내에 수증기를 주입하였다. 활성화 공정에서는 활성화온도, 활성화시간, 수증기 주입량을 변화시키며 실험하였으며, 표 2는 활성탄 제조 공정의 조건들을 요약하여 보여주고 있다.
각 원료물질로부터 제조된 활성탄은 ASAP 2420 (Micromeritics, USA) 장치를 사용하여 BET 표면적 및 기공 부피를 측정하였다. 77K 질소가스를 이용하여 미세기공 부피는 t-plot법으로 산정하였으며, 중기공 부피는 BJH (Barrett Jouner Halenda)법으로 산정하였다. 본 연구에서 제조된 활성탄이 중기공이 크게 분포하여 이력현상 (hysteresis)이 크게 발생하여 BJH법 중 흡착식을 이용하여 기공의 부피를 산정하였다. 반면에 활성화 이전 탄화물의 경우 분석 시 낮은 상대압력 영역에서 BET 표면적 측정을 위한 압력이 일정해지지 않아 측정이 불가하였다. 따라서 각 원료물질의 탄화물에 대해서는 요오드 흡착능을 통하여 탄화물의 표면적을 간접적으로 확인하였다 (Kim, 2008; Park et al., 2005). 또한 각 원료물질로부터 제조된 탄화물 및 활성탄은 SEM (Scanning Electron Microscope, LEO-1530, Carl Zeiss, Germany) 분석을 통하여 기공의 발달 정도를 알아보았다.
2. 3 수은 흡착 실험
최적조건에서 제조된 활성탄의 수은 흡착 효율을 상용화된 수은 흡착용 활성탄과 비교하기 위하여 그림 3과 같은 실험장치를 구성하여 수은 흡착실험을 수행하였다. 각 30 mg 활성탄 시료는 6 g 이산화규소 (SiO2)와 혼합한 후, 내경 1.27 cm의 고정층 반응기 안에 넣었다. 또한 고정층 반응기는 강제순환오븐 (OF-22GW, Jeio Tech, Korea) 안에 넣어 140˚C의 일정한 온도가 유지되도록 하였다. 140˚C 실험온도는 활성탄 분말의 분사 기술이 적용되는 배기가스의 온도를 모사한 것이다.
활성탄 시료에 주입하는 가스는 연소시설의 배기가스를 모사한 가스로 12% 이산화탄소 (CO2), 5% 수증기 (H2O), 5% 산소 (O2), 500 ppm 이산화황 (SO2), 200 ppm 일산화질소 (NO), 70∼80 μg/m3 원소수은 (Hg0)의 조성을 가지고 있으며, 전체 모사가스의 유량은 1 L/min이다. 다만 실제 연소시설 배기가스에는 염화수소 (HCl)가 존재하는데, 이는 활성탄의 원소수은 흡착 효율을 증가시키는 데 큰 역할을 하는 가스로 알려져 있다. 본 연구에서 사용하는 활성탄은 상용화된 활성탄과 최적조건에서 제조된 활성탄이어서 고효율의 수은 흡착 능력이 예상되므로, 각 시료 간의 흡착능력 비교가 용이하도록 HCl을 주입하지 않았다. 공기, 질소 (N2), 이산화탄소 (CO2), 이산화황 (SO2), 일산화질소 (NO) 실린더를 구비하여 MFC를 통해 일정유량으로 주입하여 각 성분의 농도를 유지하였다. 수증기는 증류수를 채운 삼각플라스크를 일정한 온도의 수조에 둔 후, N2를 증류수에 주입하여 수증기가 모사가스에 공급되도록 하였다. 원소수은은 수은 투과관 (VICI Metronics, USA)을 넣은 유리관을 일정한 온도의 수조에 두고, 일정 유량의 질소를 주입하여 전체 모사가스 중에 원소수은의 농도가 70∼80 μg/m3로 유지되도록 하였다.
고정층 반응기 내에 활성탄 시료를 거친 후 배출되는 가스 중 수은의 농도는 온타리오 하이드로법 (Ontario Hydro Method)으로 결정하였다. 온타리오 하이드로법은 수은분석에 일반적으로 통용되는 습식 분석법으로 산화수은과 원소수은을 분리하여 각 농도를 결정할 수 있다. 배출가스 중 원소수은의 농도는 가스상 수은 분석기 (RA-915M, Lumex, Cyprus)를 통하여 연속적으로 측정하였다. 실험을 시작하기 전에 모사가스는 우회경로 (bypass line)를 통하여 흐르도록 하여, 수은농도가 70∼80 μg/m3로 일정해지는 것을 확인한 후에, 모사가스를 시료에 주입하여 실험을 시작하였다. 원소수은 주입농도 ([Hg0]in)는 실험 전 우회경로를 통하여 주입되는 모사가스 중의 원소수은 농도를 가스상 수은 분석기로 측정하여 결정하였다. 원소수은 배출농도 ([Hg0]out)는 활성탄 시료를 거친 후 배출되는 가스 중 수은의 농도가 일정해지는 시점인 실험시작 20분 이후부터 40분까지의 원소수은 농도를 평균하여 결정하였다. 이로부터 활성탄 시료의 원소수은 흡착 효율은 아래의 식으로 구하였다.
(1) |
3. 실험 결과 및 고찰
3. 1 탄화실험 결과
탄화조건이 소나무 톱밥 탄화물의 비표면적에 미치는 영향을 요오드 흡착능을 통해 살펴보았다. 나무를 구성하고 있는 셀룰로오스, 헤미셀룰로오스, 리그닌과 같은 성분들은 서로 다른 온도범위에서 분해가 이루어지므로 탄화온도에 따라 탄화물의 비표면적에 차이가 날 수 있다. 탄화온도에 따른 소나무 톱밥 탄화물의 요오드 흡착능 결과를 나타낸 그림 4를 보면, 1.5시간의 동일한 탄화시간에서 500˚C, 600˚C에서 제조된 탄화물은 탄화온도 상승과 함께 요오드 흡착능이 149 mg/g에서 357 mg/g으로 증가하였다. 반면에 600˚C와 650˚C에서 제조된 탄화물의 요오드 흡착능은 서로 큰 차이가 없었다. 따라서 600˚C에서 소나무 톱밥 내 대부분의 휘발성분들이 제거되는 것으로 나타났다. 그림 5는 최적 탄화온도인 600˚C에서 탄화시간에 따른 요오드 흡착능을 나타낸 것으로, 0.5∼1.5시간 범위에서는 탄화시간 증가에 따라 요오드흡착능이 증가한 반면, 1.5시간 이상에서는 요오드 흡착능이 감소하였다. 따라서 탄화시간 1.5시간까지는 원료물질 내 휘발분이 제거되면서 기공이 형성되지만, 그 이상에서는 기공벽이 붕괴되어 비표면적이 오히려 감소하는 것으로 판단된다.
그림 6, 7은 석탄 시료에 대하여 탄화온도와 탄화시간에 따른 요오드 흡착능을 보여준 것이다. 그림 6에서 보는 바와 같이 탄화온도 700˚C에서 가장 높은 요오드 흡착능을 보였으나, 요오드 흡착능의 값은 45 mg/g으로 소나무 톱밥 시료보다 매우 낮은 값을 보였다. 또한 그림 7에서와 같이 탄화시간 1시간에서는 0.5시간보다도 낮은 요오드 흡착능 값을 보여, 석탄시료는 탄화공정에 따른 비표면적 증가가 매우 미미한 것으로 나타났다. 이는 이미 석탄 생성과정에서 오랜 기간 탄화공정과 유사한 과정을 거쳤기 때문일 것이다 (Marsh and Rodriguez-Reinoso, 2006).
이상의 탄화실험을 통하여 소나무 톱밥은 600˚C, 1.5시간에서 최대 요오드 흡착능을 나타내었으며, 석탄은 700˚C, 0.5시간에서 최대 요오드 흡착능을 나타내었다. 탄화실험에서 구한 탄화 최적조건은 이후의 활성탄 제조에 적용하여 활성화 조건에 따른 활성탄 특성을 조사하였다.
그림 8, 9는 소나무 톱밥과 석탄의 원 시료와 각각의 최적조건에서 탄화과정을 거친 후 제조된 탄화물의 SEM (Scanning Electron Microscopy) 분석 결과를 보여주고 있다. 탄화 전의 시료는 2만 배율에서 부드러운 평면 형태를 보이며, 탄화 공정을 거친 후에는 탄화물의 표면이 다소 거칠어졌다. 따라서 SEM 결과를 볼 때 각 원료물질로부터 제조된 탄화물은 표면상으로 일그러진 형태를 보일 뿐, 기공은 거의 생성되지 않는 것을 확인할 수 있다.
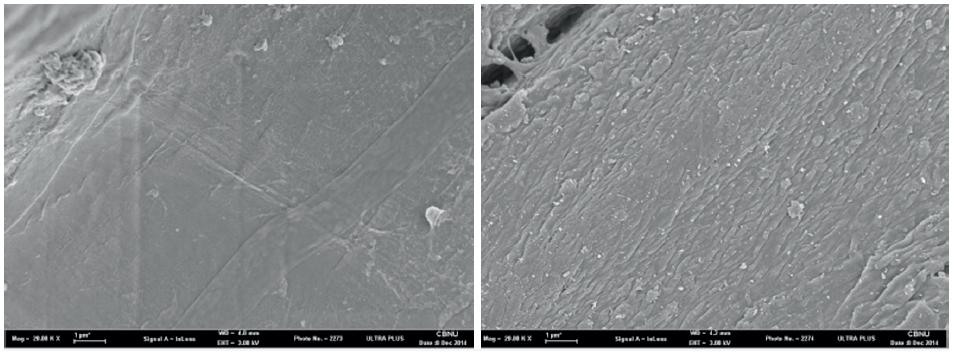
SEM images of the pinewood sawdust sample (left) and the pinewood char (right) produced at 600˚C during 1.5 hr [Magnification: 20,000×].
3. 2 활성탄 제조 실험 결과
탄화실험에서 구한 최적 탄화조건을 적용하고, 수증기를 이용한 활성화 과정을 통하여 활성탄을 각각 제조하였다. 본 연구의 활성화공정에서 사용되는 수증기는 탄화물의 탄소성분과 반응을 통해 탄소를 소비함과 동시에 미세한 기공을 형성하는 단계로 활성화 온도, 활성화 시간, 수증기 주입량은 반응속도 및 반응량에 영향을 미치는 중요한 인자가 된다. 따라서 탄화 최적조건을 적용하고, 활성화 온도, 활성화 시간, 수증기 주입량을 변화시켜 최적의 활성탄 제조조건을 찾고자 하였다. 그림 10과 11은 활성화 시간과 수증기 주입량을 각각 1 hr, 5.4 g/g·hr으로 고정하였을 때, 활성화온도에 따른 비표면적과 기공분포를 보여주는 것이다. 활성화온도에 따른 비표면적을 보면, 900˚C에서 1128 m2/g으로 가장 높고, 활성화온도 증가에 따라 점차 감소하여 1100˚C에서는 623 m2/g을 나타내었다. 이는 900˚C 이상의 온도에서는 활성탄 과정에서 이루어진 기공의 일부가 오히려 파괴되는 현상이 나타나는 것으로 판단된다 (Rambabu et al., 2013).
그림 11에서는 또한 각 활성화 온도에서 제조된 활성탄 1 g당 미세기공 (micropore), 중기공 (mesopore)의 부피를 보여준다. 900˚C에서 제조된 활성탄의 경우 미세기공과 중기공 부피가 각각 0.388 cm3/g, 0.579 cm3/g으로 가장 높았다. 그러나 비표면적 결과와 마찬가지로 활성화 온도가 증가함에 따라 미세기공 및 중기공 부피 모두 감소하며, 특히 중기공이 활성화 온도 증가로 인해 큰 폭으로 감소하였다. 이는 활성화 온도 증가함에 따라 중기공을 형성하는 탄소벽이 무너져 중기공 부피와 비표면적이 감소하는 현상을 보여준다.
그림 12는 900˚C 활성화 온도와 1 시간의 활성화시간에서 수증기 주입량 변화에 따른 비표면적 변화를 보여준다. 수증기 주입량이 1.4 g/g·hr에서 5.4 g/g·hr으로 증가함에 따라 제조된 활성탄의 비표면적은 78 m2/g에서 1128 m2/g으로 급격하게 증가하다가 6.3 g/g·hr의 수증기 주입량에서는 692 m2/g으로 감소하였다. 수증기는 탄소와의 반응을 통하여 기공을 형성하는데 수증기 양이 증가함에 따라서 비표면적이 증가하다가 수증기 주입량 6.3 g/g·hr에서는 오히려 기공 벽을 구성하는 탄소성분이 손실되어 비표면적이 감소한 것으로 판단된다.
또한 그림 13에 나타낸 수증기 주입량에 따른 미세기공과 중기공의 부피에서도 수증기 주입량이 증가함에 따라 미세기공과 중기공의 부피가 함께 증가하다가 수증기 주입량 6.3 g/g·hr에서는 기공의 부피가 감소하였다. 특히 중기공의 부피가 급격히 감소한 것으로 보아 수증기 주입량 6.3 g/g·hr에서 중기공이 붕괴되는 현상이 주로 일어났을 것으로 예상되며 이로 인하여 비표면적이 감소하였을 것으로 판단된다.
이후 900˚C의 활성화온도와 5.4 g/g char·hr 수증기 주입량을 최적조건으로 하여 활성화 시간에 따른 영향을 살펴보았다. 그림 14에서 보면 활성화시간이 0.5시간에서 1.5시간으로 증가함에 따라 비표면적이 크게 증가하다가 2시간에서는 비표면적이 감소하였다. 따라서 비표면적의 결과로서는 1.5시간의 활성화 시간이 타당한 것으로 나타났다. 그러나 그림 15에 나타낸 기공부피의 변화를 보면 활성화 시간이 1시간에서 1.5시간으로 증가함에 따라 중기공은 크게 증가하였으나 미세기공은 오히려 감소한 것으로 나타났다. 이는 활성화 시간이 1시간에서 1.5시간으로 진행되면서 소나무 활성탄의 미세기공이 중기공으로 전환된 것으로 미세기공의 일부가 붕괴되어 나타난 현상으로 판단된다. 또한 경제적인 측면을 고려하면 활성화 시간이 짧은 것이 유리하므로 활성화 시간 1시간을 최적조건으로 결정하였다.
이상의 결과들로부터 활성화온도, 활성화시간, 수증기주입량은 활성탄의 비표면적 및 기공부피를 증가시키는 역할을 할 수 있으나, 일정값 이상에서는 형성된 기공이 합쳐지거나 보다 큰 기공을 형성하여 비표면적과 기공부피를 오히려 감소시키는 역할을 하는 것으로 나타났다. 소나무톱밥에 대해서는 900˚C 활성화온도, 5.4 g/g char·hr 수증기 주입량, 1시간 활성화시간이 최적조건으로 나타났다. 또한 최적조건에서 발달된 활성탄의 기공은 그림 16의 SEM 결과에서도 확인할 수 있었다.
소나무 톱밥 원료를 이용한 활성탄 제조에서와 마찬가지로 활성화온도, 수증기 주입량, 활성화시간을 변화시킴에 따라 석탄 원료의 활성탄을 제조하였다. 먼저 활성화온도를 800, 900, 950˚C로 변화시켰을 때 제조된 활성탄의 비표면적은 그림 17에서와 같이 421, 629, 721 m2/g으로 증가하였다. 또한 그림 18에서와 같이 기공의 부피도 활성화온도 증가에 따라 증가하는 경향을 보인다. 900˚C와 950˚C에서 중기공의 부피는 0.089 cm3/g에서 0.181 cm3/g으로 증가하였으나, 미세기공의 부피는 0.234 cm3/g에서 0.224 cm3/g로 오히려 감소하는 경향을 나타내었다. 이 온도 구간에서 미세기공의 일부가 중기공으로 전환되었음을 보여준다. 그리고 경제적인 측면을 고려한다면 활성화온도가 낮은 것이 유리하므로 활성화온도 900˚C를 최적조건으로 결정하였다.
활성화온도 900˚C를 최적온도 조건으로 정하고, 수증기 주입량에 대한 영향을 살펴보았다. 소나무 톱밥에 대해서는 5.4 g/g·hr에서 가장 높은 비표면적과 기공부피를 보인 점을 고려하여 5∼8 g/g·hr의 범위에서 수증기량을 1 g/g·hr씩 증가시키며 실험하였다. 그 결과 그림 19과 20에서와 같이 이 범위 내에서는 비슷한 수준의 비표면적과 기공부피를 나타내었다. 그 중에서도 6 g/g·hr, 7 g/g·hr에서 높은 값을 나타내어 수증기 주입량의 최적조건으로 결정되었다.
마지막으로 활성화온도 900˚C와 수증기 주입량 6 g/g·hr을 최적조건으로 고정한 후 활성화시간을 0.5∼2 시간의 범위에서 0.5시간 간격으로 변화시키며 실험하였다. 그 결과 그림 21, 22에서 보는 바와 같이 1.5시간까지는 비표면적과 기공부피가 지속적으로 증가하다가 2시간에서는 모두 감소하는 결과를 확인하였다. 비록 적은 값이지만 1.5시간에서 2시간으로 증가되는 구간에서는 비표면적, 중기공 부피, 미세기공 부피가 모두 감소하여 과도한 활성화에 따른 기공 및 비표면적의 감소를 확인할 수 있었다. 따라서 석탄을 원료로 활성탄을 제조할 때에는 활성화온도 900˚C, 수증기 주입량 6 g/g·hr, 활성화시간 1.5시간이 최적조건으로 나타났다. 소나무 톱밥을 원료로 활성탄을 제조할 때의 최적조건이 활성화온도 900˚C, 수증기 주입량 5.4 g/g·hr, 활성화시간 1시간이었는데, 활성화시간이 1.5시간일 때에도 높은 수준의 비표면적과 기공부피를 유지하였음을 감안한다면 원료에 관계없이 활성탄 제조의 최적조건이 서로 유사하게 나타났다.
석탄을 원료로 최적조건에서 제조된 활성탄의 기공은 그림 23의 SEM 결과에서도 확인할 수 있는데, 같은 배율의 소나무 톱밥 원료 활성탄의 결과인 그림 16과 비교하여 볼 때 석탄 원료 활성탄에서 미세기공이 더 발달하였음을 육안으로도 확인할 수 있다.
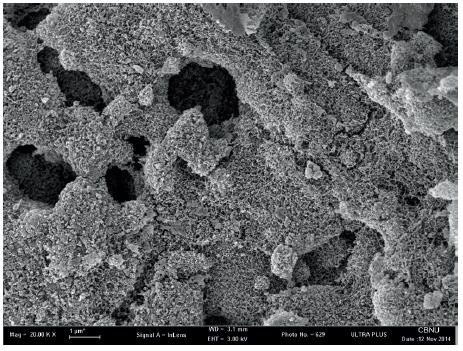
SEM image of the activated carbon produced from coal at optimum conditions [Magnification: 20,000×].
표 3에서는 최적조건으로 제조된 소나무 톱밥 원료 활성탄, 석탄 원료 활성탄과 국외에서 상용화된 활성탄 (GL-50)의 특성을 서로 비교하여 나타내었다. 소나무 톱밥 원료 활성탄과 석탄 원료 활성탄의 특성을 먼저 비교해보면, SEM 결과를 통해 설명한 바와 같이 중기공 부피/미세기공 부피의 비가 1.49와 0.38로 큰 차이를 보였다. 또한 비표면적 값에서도 소나무 톱밥 원료 활성탄이 1128 m2/g, 석탄 원료 활성탄이 629 m2/g으로 서로 큰 차이를 보였으나 이는 석탄이 소나무 톱밥보다 원시료에서 재함량이 높은 것에 기인한다. 또한, 본 연구에서 제조된 활성탄들은 국외에서 상용화된 활성탄 수준의 비표면적 및 기공부피 값을 가지는 것으로 나타났다.
3. 3 수은흡착 실험 결과
실험실에서 제조된 소나무 톱밥 원료 활성탄과 석탄 원료 활성탄의 수은 흡착 능력을 평가하기 위하여 최적조건에서 제조된 각각의 활성탄과 국외에서 상용화된 활성탄 (GL-50)을 그림 2의 실험시스템을 이용하여 시험하였다. 그림 24에서 보는 바와 같이 모사가스를 시료에 주입하자 동시에 원소수은의 배출농도가 급격히 감소함을 확인할 수 있다. 그리고 실험 시작 후 약 20분 이후에는 모든 활성탄이 95% 이상의 흡착 효율을 보임을 확인할 수 있다. 따라서 실험실에서 제조된 소나무 톱밥 원료 활성탄과 석탄 원료 활성탄은 국외에서 상용화된 활성탄 수준의 높은 수은 흡착 능력을 지니고 있음을 확인할 수 있었다. 소나무 톱밥 원료 활성탄이 다른 활성탄들에 비하여 안정화되는 데 상대적으로 많은 시간이 걸리는데, 이것은 추가적인 연구를 통하여 원인을 규명할 필요가 있다.
4. 결 론
본 연구에서는 수은 흡착제 제조를 목적으로 소나무톱밥과 석탄을 원료로 하여 활성탄을 제조하였고, 제조조건에 따른 활성탄의 특성을 조사하였다. 그리고 제조된 활성탄의 수은 흡착성능을 국외에서 상용화된 활성탄과 비교 평가하였다. 제조된 활성탄은 비표면적, 미세기공 부피, 중기공 부피를 기준으로 사전평가하였고, 이 값들이 높은 활성탄을 제조하기 위해 필요한 최적의 탄화조건과 활성화조건을 결정하였다. 최적조전을 결정하는 과정은 먼저 최적의 탄화조건을 결정한 후에, 활성화조건을 결정하는 순서로 하였다. 최적 탄화조건에 대한 실험 결과, 소나무 톱밥은 석탄에 비하여 상대적으로 긴 시간의 탄화과정이 필요한 것으로 나타났다. 이후 활성화 과정은 각 원료에 대한 최적 탄화조건을 적용하여 진행한 결과, 소나무톱밥과 석탄은 서로 유사한 활성화 최적조건을 나타내었다. 그러나 소나무톱밥 원료 활성탄은 중기공 부피가 매우 높은 특징을 가지고 있었다. 최적조건에서 제조된 활성탄의 수은 흡착 성능을 시험한 결과 소나무톱밥 원료 활성탄과 석탄 원료 활성탄 모두에서 상용화된 활성탄 수준의 높은 수은 흡착 효율을 확인할 수 있었다. 이는 국내의 기술로도 수은 흡착용 활성탄의 제조가 가능함을 보여주는 결과이며, 다른 원료의 활성탄에 대한 수은 흡착 특성 이해를 위한 추가 연구를 통하여 더욱 효율적이고 경제적인 수은 흡착제 제조가 가능할 것으로 예상된다.
Acknowledgments
이 논문은 2013년도 충북대학교 학술연구지원사업의 연구비 지원에 의하여 연구되었음.
References
- Ahn, H.S., (2004), Study on the removal method of mercury in the flue gas after coal combustion, Hanbat University, Master’ thesis.
- Cha, S.Y., (2002), Vapor phase mercury removal by sulfur impregnated activated carbons, Daejeon University, Master’ thesis.
-
Ghani, W., A. Mohd, G. Silva, R.T. Bachmann, Y.H. Taufiq- Yap, U. Rashid, and A Al-Muhtaseb, (2013), Biochar production from waste rubber-wood-sawdust and its potential use in C sequestration: chemical and physical characterization, Ind, Crop. Prod, 44, p18-24.
[https://doi.org/10.1016/j.indcrop.2012.10.017]
- Hong, H.J., (2013), Activity of gaseous elemental mercury by transition metal chloride loaded V2O5-WO3/TiO2- based catalysts, Kyungil University, Master’ thesis.
-
Kang, S.W., S.H. Shim, S.H. Jeong, J.H. Jung, and S.S Lee, (2012), Mercury emission characteristics from cocombustion of coal and sludge, J. Korean Soc. Atmos. Environ, 28(2), p182-189, (in Korean with English abstract).
[https://doi.org/10.5572/KOSAE.2012.28.2.182]
- Kim, J.M., (2008), Study on development of activated carbons from waste timbers and their adsorption characteristics, The University of Suwon, Doctoral dissertation.
-
Lee, S.H., and Y.O Park, (2003), Gas-phase mercury removal by carbon-based sorbents, Fuel process. Technol, 84, p197-206.
[https://doi.org/10.1016/S0378-3820(03)00055-9]
- Lee, S.J., (2004), Studies on the speciation and adsorption mechanism of mercury in the combustion flue gas, Yonsei University, Doctoral dissertation.
- Marsh, H., and F. Rodriguez-Reinoso, (2006), Activated carbon, Amsterdam, London, Elsevier.
- Park, K.S., (2008), Emission and distribution characteristics of mercury species at combustion and incineration facilities, Yonsei University, Doctoral dissertation.
- Park, Y.C., K.J Cho, and J.H. Choi, (2005), Production and CO2 adsorption characteristics of activated carbon from bamboo by CO2 activation method, Korean Chem. Eng. Res, 53(1), p146-152.
-
Rambabu, N., R. Azargohar, A.K. Dalai, J. Adjaye, (2013), Evaluation and comparison of enrichment efficiency of physical/chemical activations and functionalized activated carbons derived from fluid petroleum coke for environmental applications, Fuel Process. Technol, 106, p501-510.
[https://doi.org/10.1016/j.fuproc.2012.09.019]
-
Skodras, G., I Diamantopoulou, A. Zabanioutou, G. Stabropoulos, G.P. Sakellaropoulos, (2007), Enhanced mercury adsorption in activated carbons from biomass materials and waste tires, Fuel Process. Technol, 88, p749-758.
[https://doi.org/10.1016/j.fuproc.2007.03.008]
-
Vuthaluru, H.B., (2003), Thermal behaviour of coal/biomass blends during co-pyrolysis, Fuel Process. Technol, 85, p141-155.
[https://doi.org/10.1016/S0378-3820(03)00112-7]